 |
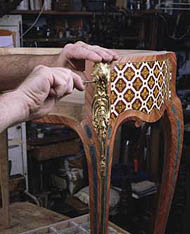
 |
 |
A French craftsman works on a copy of an 18th-century writing table in the Getty Museum's collection. |
 |
Throughout the 1700s in France, the making of furniture was an elaborate process involving a variety of craftsmen, from the cabinetmaker to the bronze founder to the finisher. The environment of these Parisian artisans, their training, neighborhoods, design sources, and patrons all combined to influence the final products. Much of the veneered furniture in the Getty's collection was the result of this collaboration.
To illustrate the steps in making such furniture, the Getty Museum commissioned three reconstructions, in varying stages of completion, of a mid-18-century writing table from its collection. The three copies were made in Paris by contemporary craftsmen using tools and techniques similar to those employed in the workshop of Jean-FranÇois Oeben, where the original table was made.
|
 |
Table reconstructions: Alain Guéroult, Hardouin Burrus, Andréa Coerdt, and Pierre Ramond, under the supervision of Michel Jamet, L'Ebénisterie Michel Jamet, Paris. Gilt-bronze mount casting: Atelier Amaury. Gilt-bronze mount gilding: Atelier Deville. Leather preparation: Atelier Larking-Coste and Perrin. Leather decoration: Atelier Lemerle. Photographs: Thomas Hennocque
|
 |
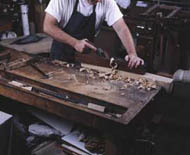
 |
 |
Wood is planed into flat, even boards. |
 |
 |
The table is built with affordable, locally available wood as well as rare, imported woods. After a tree is cut down and into planks, the cabinetmaker uses planes to smooth the planks into straight, even boards. Boards of local wood are used to build the structure, or carcass.
Preparing the veneer
The surface wood decoration is made from a plank that has been cut into thin sheets, or veneers. Colorful veneers are often crafted from rare, expensive woods imported to France. Once cut, the veneers are prepared with smoothing planes and scrapers.
|
 |
To build the structure, or carcass, of a table, the cabinetmaker works from drawings and patterns to size and shape the parts. The cabinetmaker uses two principle joints: the mortise-and-tenon, and the dovetail.
After the joints are cut, the frame is fitted together and patterns are used to trace contours on the sides of the legs. Saws, chisels, spokeshaves, and rasps give the table its form.
|
 |
The carcass of the table is completed and prepared for the surface decoration. The cabinetmaker uses chisels, rasps, and scrapers to refine the undulating surface. He contours the sides and the legs and smooths the joints where they meet.
Once the carcass is shaped, the cabinetmaker builds the drawer and prepares the top and writing surface.
|
 |
 |
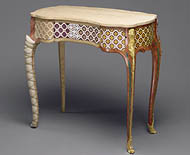
 |
 |
The application of marquetry is shown in stages on this copy. |
 |
 |
|
 |
|
 |
|
Creating marquetry
The cabinetmaker uses a drawing to create a cutting pattern for each piece of the marquetry. He then cuts individual pieces of the design from appropriately colored wood and assembles the composition. The marquetry is adhered to the curved shape of the leg with a bag of hot sand, which presses the marquetry evenly on the curved surface, and activates the heat-sensitive glue. The drawer shows the progression of the veneer application, beginning with the background, then adding the trellis motif, and finally the flowers.
The finishing touches
Once the marquetry is applied, it is brought to life with varnish. The leather writing surface and the gilt-bronze mounts complete the ensemble.
|
 |
This table, made in the mid-18th-century, served as the model for the reproductions above. The veneer and marquetry are characteristic of Jean-François Oeben, ébéniste du roi (cabinetmaker to the king). The modern copies of the table look different from the original because it was exposed to light over the centuries, which caused the wood to discolor and fade.
Baskets of flowers, like the one seen on the table's top, were a recurring motif in French decorative arts and Oeben was a master of translating this theme into marquetry. The trellis pattern on the sides of the table may derive from Japanese lacquer designs, which were highly fashionable in the 1700s. In all, the oak carcass is veneered with 15 types of wood.
|
 |
Credits: Table reconstructions: Alain Guéroult, Hardouin Burrus, Andréa Coerdt, and Pierre Ramond, under the supervision of Michel Jamet, L'Ebénisterie Michel Jamet, Paris. Gilt-bronze mount casting: Atelier Amaury. Gilt-bronze mount gilding: Atelier Deville. Leather preparation: Atelier Larking-Coste and Perrin. Leather decoration: Atelier Lemerle. Photographs: Thomas Hennocque
|
 |