 |
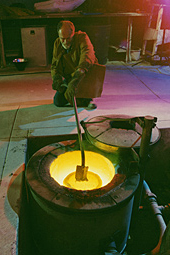
 |
 |
Working with molten bronze |
 |
Dutch artist Adriaen De Vries became renowned in his lifetime for the innovative compositions and technical virtuosity of his bronze sculpture. He made Juggling Man around 1610, at a time when technical innovations in casting would have offered a safer approach than the method he chose.
De Vries practiced the more traditional direct lost-wax approach, in which the original model sculpted of clay and wax becomes encased in a mold. If the artist ran into a problem during the next stage of casting with molten bronze, he would have had to start the creative process all over again. The model would have been destroyed.
This exhibition and accompanying photographs and videos demonstrate the process of bronze casting as de Vries practiced it for Juggling Man. It is explained in three stages: modeling, casting, and finishing.
|
 |
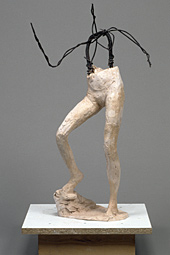
 |
 |
Modeling clay on an armature |
 |
 |
De Vries built an iron-rod armature and shaped it to form the juggler's posture. To this metal structure he applied wet clay, modeling it to create the general form of the man's body. After the clay dried, De Vries coated it with a layer of wax, which he modeled for fine details. He formed the figure's right foot, hands, and juggling plates entirely out of wax.
Once the model was complete, De Vries prepared it for casting. He attached a network of wax rods, called "sprues" and a wax "pouring cup." These additions would not be part of the final sculpture, but enabled the flow of molten materials during the casting process.
|
 |
De Vries applied a mixture of heat-resistant clay and other materials, called the "investment," to the sprued model. In the foundry, the investment was turned upside down in a kiln and heated. The wax layer surrounding the clay core melted out, creating a cavity inside the investment in the shape of the juggling figure.
The melted sprues created channels that would serve a dual purpose, allowing gases to escape and enabling the molten bronze to flow evenly throughout the sculpture. Once the wax had melted, the investment was turned right side up, so that molten bronze could be poured into it from the top.
|
 |
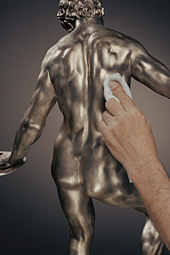
 |
 |
Polishing the cast sculpture |
 |
 |
After the metal had cooled and hardened, the investment material was removed, revealing the bronze with its attached sprues. De Vries then removed the sprues and cleaned off the sculpture's dark, sooty outer layer. He would have patched holes and repaired any flaws.
De Vries may have reworked minor details with a chisel, such as the juggler's finger- and toe-nails. (Compared to many other bronze sculptors, he did not tend to do much "chasing" or sharpening of details after casting.) Then he gave the surface a smooth, reflective shine by polishing it.
One prominent aspect of finishing a sculpture is to produce a surface color or "patina" with chemicals. He did not create the green patina, however. It formed over time as the sculpture was displayed outdoors.
|
 |
Turning to analytical techniques such as X-radiography sheds light on De Vries methods. For example, one can see the iron-rod structure that supports the clay model. X-rays also show the even distribution of bronze throughout the hollow cast, attesting to the artist's craftsmanship.
Juggling Man is a variation on a classical sculpture of a dancing faun, which De Vries changed into a juggler. The act of juggling was known by the same term in German (the artist's adopted language) used to describe artistic virtuosity. It's possible that Juggling Man is a comment on the sculptor's own artistry, with a bellows at his feet to suggest the stoking of foundry fires.
|
 |